Автор: эксперт-менеджер Халецкая Ирина Игоревна
Для кого: операторов, наладчиков, мастеров механических цехов,
технологических служб
Заготовка в патроне, управляющая программа написана, инструмент подобран, но как его привязать? Без паники, сейчас будем разбираться!
Привязка инструмента — это процесс определения положения режущей кромки инструмента относительно машинного нуля станка. Она необходима для обеспечения точности обработки деталей, предотвращения ошибок при работе и возможных столкновениях рабочих органов станка. Кстати, о причинах столкновений на станках и способах их предотвращения мы подробно рассказали в этой статье.
Методы привязки инструмента
Существует два метода привязки инструмента:
-
Ручная привязка. Этот метод предполагает привязку режущей кромки на касание к детали вручную. Он является самым простым и доступным, но требует высокой квалификации оператора и может привести к ошибкам.
-
Автоматическая привязка. В этом случае используется специальное оборудование, которое самостоятельно определяет положение инструмента. Такой способ более точный и быстрый, но требует дополнительных затрат на приобретение оборудования.
Выбор конкретного способа зависит от типа станка, сложности задачи и требований к точности обработки. Однако в любом случае необходимо следить за качеством привязки инструмента, чтобы избежать брака продукции и повреждения оборудования.
Рисунок 1. Система автоматической привязки инструмента
Способы привязки инструмента
Всё чаще можно встретить на металлообрабатывающих станках полуавтоматическую или автоматическую систему привязки инструмента, например, Renishaw. Это является эффективным решением, которое помогает повысить точность, снизить риски и улучшить производительность процесса обработки. Однако не все станки оборудованы той или иной системой. Поэтому разберем ручные способы привязки.
Привязка длины инструмента (ось Z):
-
Касание. Переводим подачу в ручной режим и осторожно подводим инструмент к детали. Делаем подачу на минимум и медленно доводим, прислушиваясь к возникающему трению. Как только увидите или услышите первые признаки контакта – останавливаемся и обнуляем отсчет. Способ быстрый, но неидеальный. Подходит только для черновой обработки торца заготовки с последующим чистовым обрабатыванием.
-
Торцевание. Аккуратно подгоняем режущий инструмент к торцу заготовки, устанавливая нулевую точку немного глубже самой детали. Плавно снимаем несколько миллиметров материала, чтобы выровнять плоскость с нулевым положением станка. Важно не переборщить с глубиной – достаточно снять небольшой слой. Однако следует учитывать, что не все детали подходят для данной процедуры, и иногда торцевую грань следует оставлять без изменений.
-
Контактный способ. Если обрабатываемая деталь проводит электричество, можно использовать систему, автоматически определяющую ноль при контакте инструмента с заготовкой. Но этот метод не подходит для непроводящих материалов, таких как дерево, камень или пластик.
-
Концевые меры или щупы. Если поверхность детали нельзя обрабатывать, можно прибегнуть к концевым плиткам или щупам заведомо известных размеров. Прикладываем щуп или меру к заготовке и на минимальной подаче подводим инструмент слегка зажимая меру. Толщину плитки необходимо учесть в корректорах. Этот точный, но трудоемкий способ, который не повреждает деталь.
-
Индикатор часового типа. Очень похоже на способ с помощью датчиков типа Renishaw, только никакой автоматики. Калиброванную оправку или сам инструмент, если его гладкая часть хвостовика выступает из зажимных кулачков, устанавливают в патрон на револьверной головке. На шпинделе устанавливаем магнитный штатив с индикатором, чтобы измерительный наконечник касался цилиндрической поверхности хвостовика. Путем ручного вращения шпинделя добиваемся неподвижности стрелки – это и есть нулевая точка.
-
Штангенрейсмус. Измеряем длину фрезы или резца и вводим данные в настройки коррекции. Это не самый простой, но эффективный метод.
-
Лист бумаги. Для простых фрезерных или токарных станков можно использовать быстрый, но менее точный способ. Постепенно подводим инструмент к заготовке, пропустив между ними лист бумаги. Как только бумага зажимается - устанавливаем ноль.
Перед остановкой шпинделя обязательно выводим инструмент по оси X, не меняя положения по оси Z.
Рисунок 2. Привязка инструмента способом торцевания
При определении координаты резца по оси X толщину мерной плитки или щупа умножают на два и прибавляют к диаметру.
Привязка инструмента по оси Х:
-
Наружная обработка. Установите резец рядом с поверхностью заготовки и выполните обработку с минимальным съёмом металла. Отведите резец по оси Z. Замерьте наружный диаметр с помощью микрометра. Введите полученный диаметр в таблицу инструмента, чтобы система запомнила сдвиг по оси Х.
-
Внутренняя обработка. В первую очередь следует привязать сверло, далее выполнить отверстие в заготовке, а затем сделать расточку. Замерьте полученный диаметр нутромером. Если отверстие слишком маленькое и нутромер не подходит, можно измерить отверстие электронным штангенциркулем. Однако точность измерения может быть ниже. Введите диаметр внутреннего отверстия в таблицу инструмента.
Рисунок 3. Измерение заготовки микрометром
Точность определения диаметров зависит от точности измерительных инструментов. Для наружной обработки рекомендуется использовать микрометр с погрешностью 0,01 мм; для внутренней обработки – нутромер с такой же погрешностью.
Что делать для корректной привязки инструмента?
Для бесперебойной работы станков с ЧПУ необходима точная настройка инструмента. Правильная установка гарантирует высокую точность и эффективность производственного процесса.
Шаг 1: Подготовка инструментов
- Проверить состояние режущих кромок инструмента;
- Очистить и, при необходимости, заточить инструмент;
- Проверить соответствие инструмента техническим требованиям задачи.
На случай, если вы затрудняетесь с выбором оборудования для заточки инструмента, можете найти ответ в этой статье.
Шаг 2: Установка инструмента
- Используйте подходящие адаптеры и патроны для надежной фиксации;
- Разместите инструмент в шпинделе или в магазине инструментов.
- Измерьте точные параметры длины, диаметра, определите тип и измерьте угол режущей кромки;
- Внесите данные каждого инструмента в систему управления станком вручную или с помощью автоматизированных систем, например, посредством лазерных измерительных систем.
- Проверьте правильность занесенных параметров;
- Произведите тестовый прогон программы для проверки корректности работы инструмента;
- Убедитесь в правильной установке и соответствии заданной программе.
Более подробно про шпиндели для токарных и фрезерных станков, как выбрать подходящий и чем они различаются – можете найти тут.
Шаг 3: Замер параметров инструмента и ввод в систему управления
Шаг 4: Проверка и тестирование
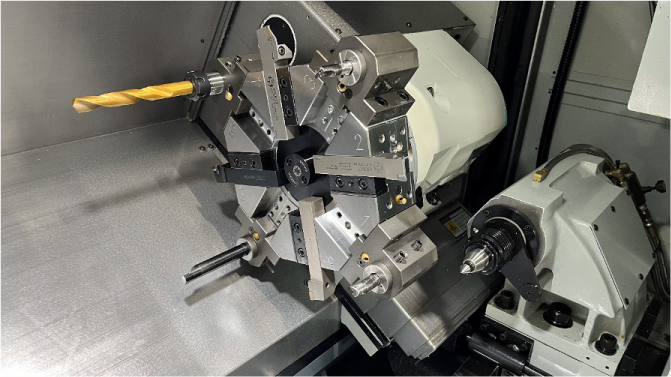
Точная привязка инструмента на станках с ЧПУ служит фундаментом для достижения безупречных результатов и максимальной производительности. Тщательно выполненная процедура сводит к минимуму погрешности, повышая эффективность обработки и сохраняя качество готовых изделий. Регулярно проверяйте состояние инструментов и корректность их работы.
Подборка оборудования